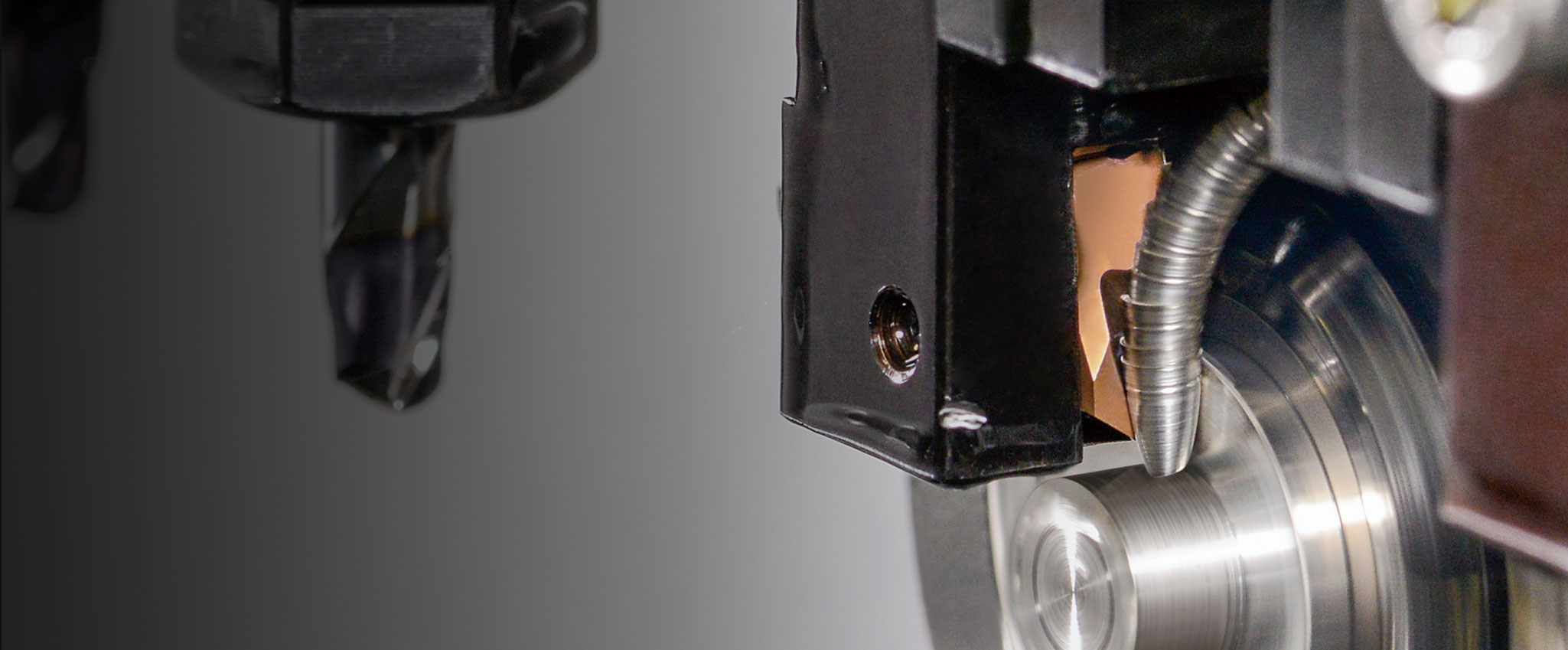
For front turning operations | Swiss CNC Lathes
Single pass machining of up to 5.0mm depth of cut
Significant reduction in cycle time due to large depth of cut capability
Chip control at both large DOC and high feed and low DOC and low feed conditions
Product video
Features
- Capable of a 5.0 mm maximum depth of cut
- NTK's unique insert design provides excellent chip control and surface finish.
- Coolant through toolholders provide additional machining stability and performance
Tooling application
Swiss CNC Lathe front turning operations
TFX chip control range
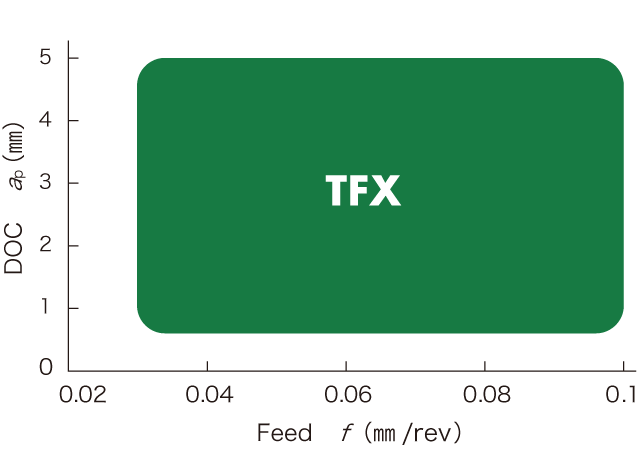
Cutting conditions
Scroll the table →
Coated grade | Material | Operation type | Cutting speed (m/min) | Feed (mm/rev) | DOC (mm) |
---|---|---|---|---|---|
ST4 | Stainless | OD Turning continuous | 50 - 120 | 0.03 - 0.1 | 0.5 - 5.0 |
DM4 | Difficult-to-cut material / titanium alloy Alloy steel / carbon steel / hardened material Non-ferrous / aluminum / plastic / general purpose |
Cutting performance
The Front Max
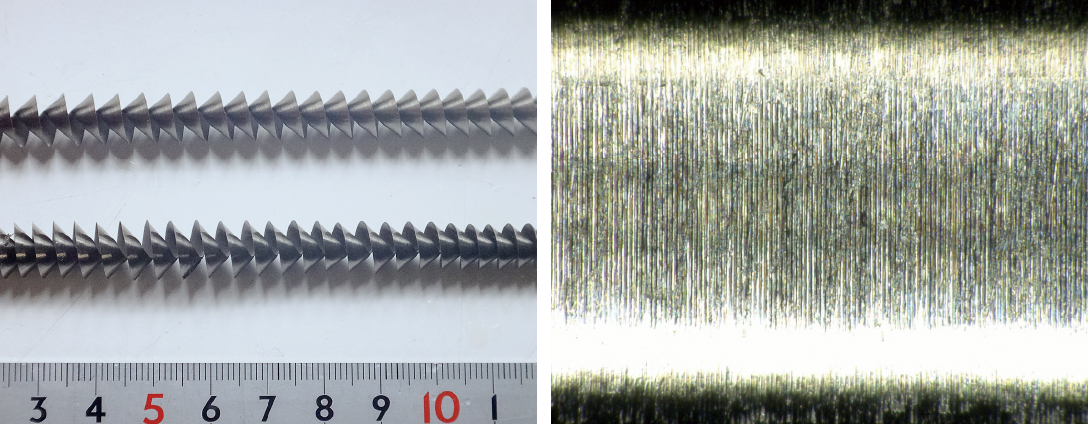
High rigidity and chip control ensures consistently superior surface finishes
- [ Cutting conditions ]
- DOC : 5.0mm Material : SUS304 vc=80m/min f=0.03mm WET
Chips from competitor's large DOC product
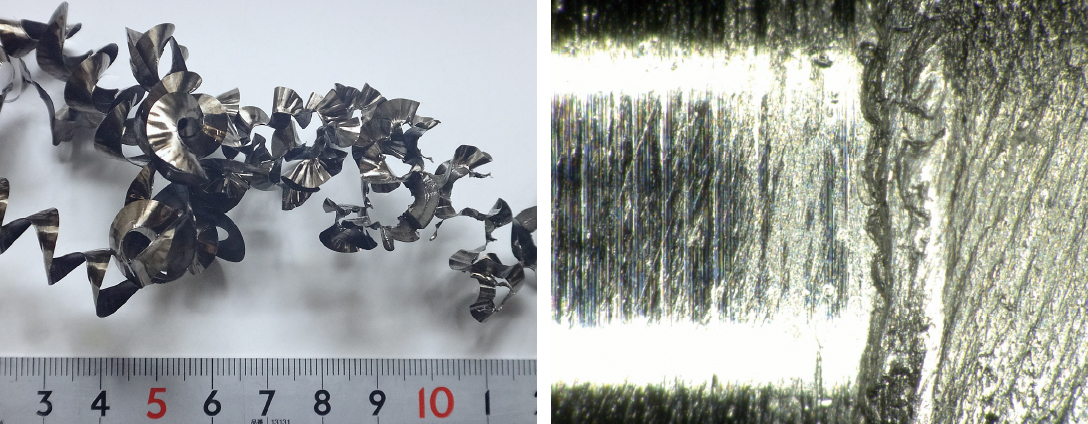
Lack of chip control leads to a poor machined surface finish
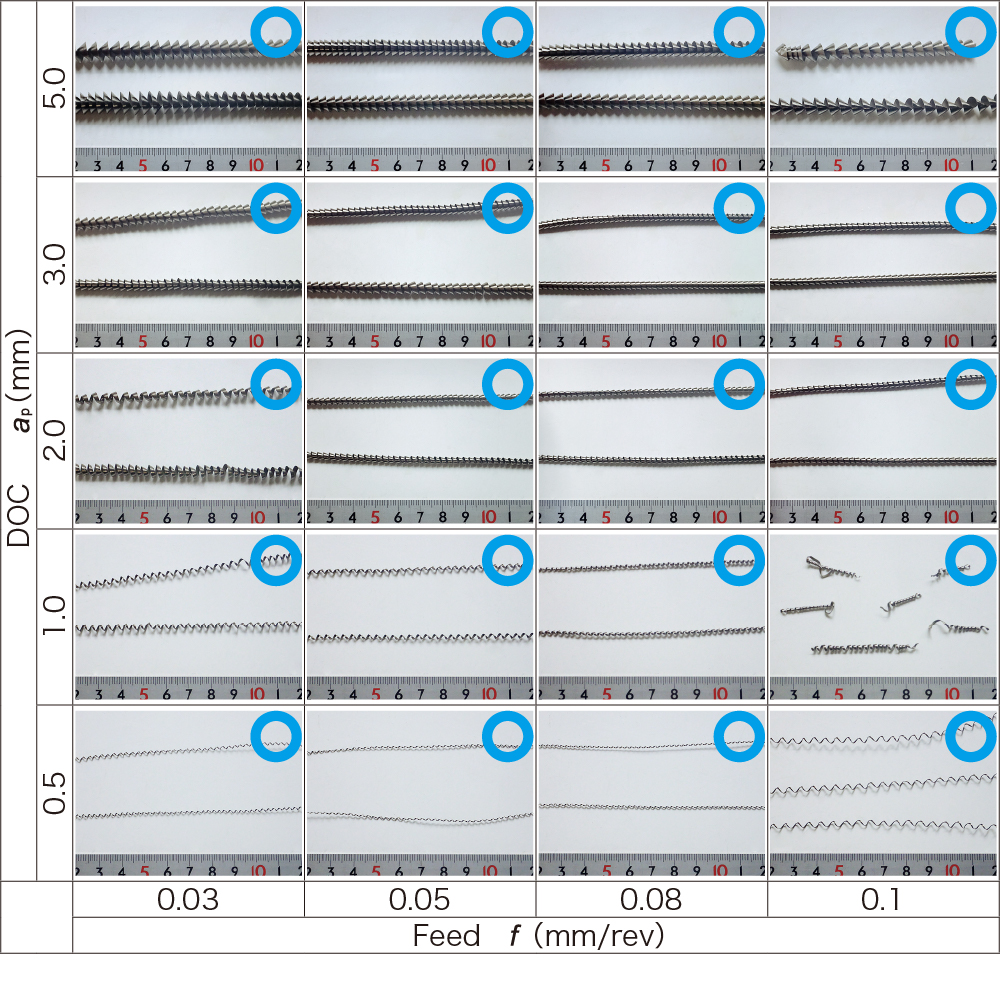
- [ Cutting conditions ]
- Material : SUS304 vc=80m/min WET
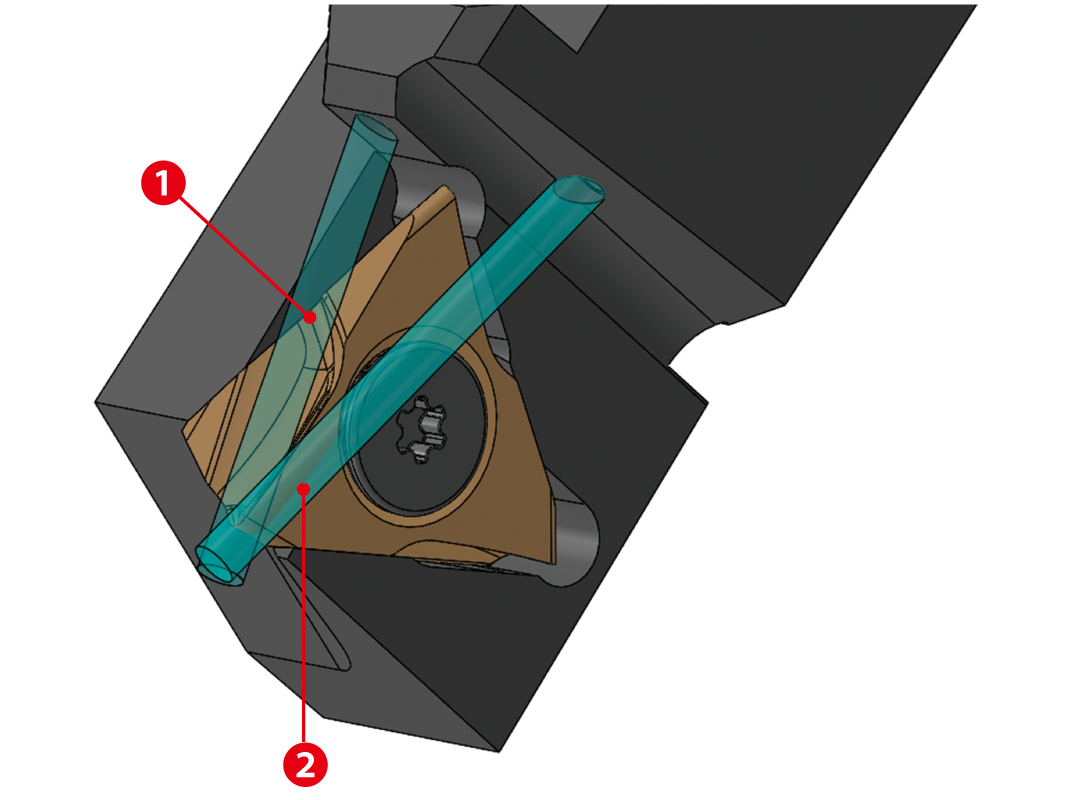
- Coolant through holders are available for TFX inserts to provide further machining stability
- ① Coolant stream directed to evacuate chips
② Coolant stream improves insert tool life
Case study
Shaft | |
---|---|
|
![]() |
|
|
|
|
|
|
|
|
The Front Max | 180 pcs / corner |
Competitor’s product | 50 pcs / corner |
The TFX "Front Max" machined at a high feeds of ap=5.0 mm while extending tool life by more than 3 x compared to the competitor's insert
Electronic component | |
---|---|
|
![]() |
|
|
|
|
|
|
|
|
ST4+ The Front Max | 160 pcs / corner |
CCGT09 Type (PVD coated carbide) |
80 pcs / corner |
The current tool required 4 passes to remove the large amount of material.
TFX machined the same material removal in 1 pass.
The feed rate was reduced to improve chip control.
Cycle time was significantly shortened and tool life increased.
Tool lineup
Please check product catalog for tooling lineup
Other recommended products
-
SPLASH seriesCoolant through toolholders | Swiss CNC Lathes
Extensive selection of styles and sizes
-
TBP/TBPA-BM chipbreakerBack turning | Swiss CNC Lathes
Unique chipbreaker provides excellent chip evacuation
-
GX chipbreakerFor grooving | Swiss CNC Lathes
Solves the issue of chips wrapping around workpiece or remaining in the groove
-
CTP/CTPA-CX chipbreakerFor cut-off operations with max. diameter up to 16mm| Swiss CNC lathes
Tightly curls chips to prevent tangling
Useful information
4 STEP-NTK Cutting Tools Lab for choosing suitable cutting tool for cut-off machining
The aspects of "chip control" that you should check when workpiece damage or poor dimensioning are detected during Swiss type CNC automatic lathe machining
Two Areas to Check When Coaxiality is Not Achieved During Swiss CNC Lathe Machining
"Two" checkpoints and measures to be checked when "Roundness" does not come out in Swiss-type CNC-automatic lathe machining-NTK Cutting Tools Lab